3-Pole Solenoid Switch,4-Pole Solenoid Switch
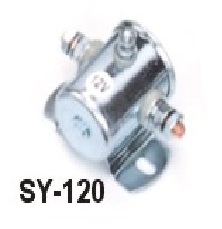
Model/Item No.:SY-120
Solenoid switches are devices that are used to control the flow of electrical current in a system. They are found in many different applications, ranging from industrial machines to home appliances. A solenoid switch is essentially an electromagnetically operated switch, meaning that it is activated by an electric current. There are two main types of solenoid switches: 3-pole and 4-pole.
A 3-pole solenoid switch has three terminals that are connected to a coil of wire. This coil is typically made of copper, and when electric current passes through it, it creates a magnetic field. This magnetic field interacts with a metal core inside of the solenoid switch, which causes the switch to be activated.
The 4-pole solenoid switch is similar to the 3-pole switch, but it has four terminals instead of three. The four poles are connected to four coils of wire, which when energized create a stronger magnetic field than the 3-pole switch. This stronger magnetic field is able to activate more powerful switches and solenoids.
When it comes to choosing the right solenoid switch for a particular application, there are several factors to consider. First, you must determine what type of switch you need: a 3-pole or a 4-pole. You must also consider the voltage and current requirements of the system, as well as the size and shape of the switch. Additionally, the environment in which the switch will be used must be taken into account. Finally, you should also consider the cost of the switch, as 3-pole and 4-pole switches can vary greatly in price.
Solenoid switches are important components for a variety of applications. They are used to control the flow of electricity in a system, and can be found in many different types of machines. It is important to understand the differences between 3-pole and 4-pole Solenoid switches, and to consider the various factors that must be taken into account when choosing the right switch for an application. By doing so, you can ensure that the switch you select is the most suitable for the job.
3-Pole Solenoid Switch,4-Pole Solenoid Switch
Solenoid switches, also known as solenoid relays or solenoid contactors, are electrical devices used to control the flow of electrical current in a circuit. They work by using an electromagnetic coil to generate a magnetic field, which then moves a switch or contact to open or close the circuit. Solenoid switches are commonly used in various applications, including automotive, industrial machinery, and electrical systems.
Here's an explanation of 3-pole and 4-pole solenoid switches:
3-Pole Solenoid Switch:
A 3-pole solenoid switch has three electrical terminals or connections. These terminals are typically labeled as "common," "normally closed," and "normally open." Here's what each of these terminals does:
Common (COM): The common terminal is where the incoming electrical power supply is connected. It is the central terminal and provides power to the solenoid coil.
Normally Closed (NC): The normally closed terminal is connected to the common terminal when the solenoid coil is not energized. When power is applied to the coil, it generates a magnetic field, causing the switch or contact to move and disconnect the normally closed terminal from the common terminal, opening the circuit.
Normally Open (NO): The normally open terminal is disconnected from the common terminal when the solenoid coil is not energized. When power is applied to the coil, the magnetic field causes the switch or contact to move and connect the normally open terminal to the common terminal, closing the circuit.
3-pole solenoid switches are commonly used in applications where a single circuit needs to be controlled, such as in automotive starter solenoids.
4-Pole Solenoid Switch:
A 4-pole solenoid switch, on the other hand, has four electrical terminals. These terminals typically include "common," "normally closed," "normally open," and an additional terminal, which can serve various functions depending on the specific application. The extra terminal can be used for purposes such as auxiliary contacts, feedback, or other control functions.
Common (COM): As with the 3-pole switch, the common terminal is where the incoming electrical power supply is connected.
Normally Closed (NC): This terminal is connected to the common terminal when the solenoid coil is not energized, and it operates in the same way as in the 3-pole switch.
Normally Open (NO): Similar to the 3-pole switch, the normally open terminal is disconnected from the common terminal when the solenoid coil is not energized, and it operates in the same way.
Additional Terminal: The fourth terminal in a 4-pole solenoid switch can have various functions, depending on the specific requirements of the application. It may serve as an auxiliary contact for additional circuit control, feedback to a control system, or other purposes as needed.
4-pole solenoid switches are used in more complex applications where multiple circuits or functions need to be controlled simultaneously or where additional feedback or control features are required.
The specific use and configuration of solenoid switches can vary widely based on the application and industry, but they are essential components for controlling electrical circuits in various devices and systems.
3-Pole Solenoid Switch:
Applications: 3-pole solenoid switches are commonly used in automotive and industrial applications. In vehicles, they are often found in starter solenoids, where they engage the starter motor when the ignition is turned.
Solenoid Coil: The solenoid coil in a 3-pole switch is typically wound with a specific number of turns to provide the necessary magnetic force to actuate the switch. The coil is energized when power is applied to it, creating the magnetic field that moves the switch.
Reliability: These switches are known for their reliability in simple circuit control tasks. They are designed to handle high-current applications and can endure numerous cycles of operation.
4-Pole Solenoid Switch:
Versatility: 4-pole solenoid switches are more versatile and flexible in terms of their applications. The additional terminal can be used for a variety of purposes, making them suitable for complex control systems.
Feedback and Control: The extra terminal in a 4-pole switch can be used to provide feedback to a control system. For example, it can indicate the status of the switch (open or closed) or provide information about the solenoid's operation.
Multiple Circuits: These switches are ideal for situations where multiple circuits need to be controlled simultaneously or where coordination between different electrical functions is required.
Auxiliary Functions: The additional terminal can also be used for auxiliary functions, such as controlling warning lights, buzzers, or other indicators related to the solenoid's operation.
Customization: Depending on the manufacturer and the specific application, 4-pole solenoid switches may have customizable configurations to meet unique requirements.
General Considerations for Both 3-Pole and 4-Pole Solenoid Switches:
Voltage and Current Ratings: Ensure that the solenoid switch is rated for the voltage and current requirements of your application. Using a switch with the correct ratings is crucial for safe and reliable operation.
Environmental Conditions: Consider the environmental conditions in which the solenoid switch will operate. Some solenoid switches are designed for harsh environments and can withstand factors like moisture, dust, and temperature extremes.
Mounting and Installation: Proper mounting and installation are essential to ensure the solenoid switch functions correctly. Follow the manufacturer's guidelines for mounting and connecting the switch.
Maintenance: Periodic maintenance may be necessary to ensure the longevity and reliability of the solenoid switch. This can include cleaning, inspecting for wear, and replacing components as needed.
Safety: When working with solenoid switches, observe safety precautions, especially when dealing with high voltages and currents. Disconnect power sources before performing maintenance or repairs.
Control Systems: Integrate solenoid switches into your control system as needed. Ensure that they are properly coordinated with other components to achieve the desired functionality.
Testing: Before putting a solenoid switch into service, perform tests to verify its operation and confirm that it functions as expected. Testing helps identify any issues before they impact the overall system.
Solenoid switches play a critical role in many electrical control systems, and choosing the right type (3-pole or 4-pole) depends on the specific requirements of your application. Proper selection, installation, and maintenance are key factors in ensuring their reliable performance.
Certainly, here are some additional considerations and information related to solenoid switches:
Common Types of Solenoid Switches:
Starter Solenoids: Starter solenoids are used in automotive applications to engage the starter motor when the ignition is turned. They play a crucial role in starting the vehicle's engine.
Contactor Solenoids: Contactor solenoids are used in industrial and commercial applications to control electrical circuits, such as motor control circuits. They often have multiple poles and can handle high currents.
Locking Solenoids: Locking solenoids are used to control locking mechanisms in various devices, including doors, cabinets, and vending machines. They are often used in access control systems.
Latching Solenoids: Latching solenoids have two stable states (on and off) and remain in the last state even after power is removed. They are used in applications where power efficiency and energy savings are critical.
Pull Solenoids: Pull solenoids operate by pulling a plunger or rod when energized. They are used in applications like printers, vending machines, and automated equipment.
Solenoid Switch Materials:
Solenoid switches are constructed using various materials, including:
Coil Windings: The coil windings are typically made of copper wire and are chosen for their electrical conductivity and ability to generate a strong magnetic field when energized.
Plungers or Pistons: These are often made of ferrous materials like iron or steel, as they are attracted by magnetic fields. When the coil is energized, it moves the plunger, which, in turn, actuates the switch or valve.
Contacts: The contacts inside the switch may be made of materials like silver or silver-plated materials, known for their good electrical conductivity and low resistance. They ensure reliable electrical connections.
Voltage and Current Ratings:
When selecting a solenoid switch, it's crucial to match its voltage and current ratings with the requirements of your application. Using a solenoid with incorrect ratings can result in unreliable operation or even damage to the switch and associated components.
Duty Cycle:
Consider the duty cycle or duty rating of the solenoid switch. Duty cycle refers to the percentage of time the solenoid can be energized and de-energized continuously without overheating. Solenoids designed for high-duty applications can operate continuously, while others are intended for intermittent use.
Control Options:
Depending on your application, you may need different control options for the solenoid switch:
Manual Control: In some cases, you may want manual control over the solenoid switch, allowing operators to activate it as needed.
Remote Control: Remote control options, such as using a relay or microcontroller, enable automation and integration into larger systems.
Proximity Sensors: In certain applications, proximity sensors can be used to trigger the solenoid switch based on the presence or absence of objects.
Environmental Considerations:
If your solenoid switch will operate in harsh environments (e.g., extreme temperatures, moisture, dust, or chemicals), choose a solenoid that is designed to withstand these conditions. Some solenoids come with IP (Ingress Protection) ratings to indicate their resistance to environmental factors.
Safety Precautions:
Always follow safety guidelines when working with solenoid switches. Ensure that power sources are properly disconnected when performing maintenance, and take precautions to prevent electric shocks and other hazards.
Customization:
For specific applications with unique requirements, consider customizing solenoid switches to meet your needs. Manufacturers may offer customization options in terms of size, shape, mounting, and electrical characteristics.
Solenoid switches are versatile components used in a wide range of applications, and selecting the right type and configuration is essential for the proper functioning of your system. It's advisable to consult with the manufacturer or a knowledgeable expert when choosing a solenoid switch for a specific application to ensure compatibility and optimal performance.
Solenoid Types and Configurations:
Linear Solenoids: These solenoids move a plunger or rod in a linear (straight-line) motion when energized. They are commonly used in applications where linear movement is required, such as in door locks, pneumatic valves, and medical devices.
Rotary Solenoids: Rotary solenoids convert electrical energy into rotary (circular) motion. They are used in applications like automotive throttle control, locking mechanisms, and industrial automation.
Push-Pull Solenoids: Push-pull solenoids combine both linear and rotary motion. They can push and pull a load in a linear direction and rotate it when needed. These are often used in applications requiring precise and reversible motion.
Tubular Solenoids: Tubular solenoids have a cylindrical shape and are suitable for applications with limited space. They are commonly used in locks, latches, and other compact devices.
Solenoid Control Mechanisms:
Direct Acting Solenoids: In direct-acting solenoids, the plunger or armature directly moves the load when the coil is energized. These solenoids offer a simple and quick response.
Pilot-Operated Solenoids: In pilot-operated solenoids, the solenoid controls a separate pilot valve, which in turn controls the flow of fluid (e.g., air or hydraulic fluid) to move the load. These are often used in applications requiring precise control.
Latching Solenoids:
Latching solenoids are designed to maintain their position (either open or closed) without continuous electrical power. They are commonly used in applications where power consumption and heat generation need to be minimized. Latching solenoids are often used in battery-operated devices and where energy efficiency is essential.
Solenoid Actuation Force:
The force produced by a solenoid is an important consideration. It should match the requirements of the application. Some solenoids are designed to provide high force for heavy-duty tasks, while others are meant for low-force, delicate operations.
Spring-Return Solenoids:
Spring-return solenoids have a built-in spring that returns the plunger or armature to its original position when the solenoid is de-energized. These solenoids are used in applications where the default state of the system is important.
Fail-Safe Solenoids:
Fail-safe solenoids are designed to return to a specific position or state in the event of a power failure or malfunction. They are often used in safety-critical applications where specific actions are required to prevent accidents or damage.
Integration with Control Systems:
Many solenoids can be integrated with control systems, such as programmable logic controllers (PLCs) and microcontrollers, to provide precise control and monitoring capabilities. Consider the compatibility of the solenoid with your control system.
Solenoid Material and Construction:
Depending on the application, you may need to choose a solenoid with specific materials and construction features, such as corrosion-resistant coatings or materials suitable for high-temperature environments.
Feedback and Position Sensors:
In some applications, it's important to have feedback on the position of the solenoid. Position sensors or encoders can be integrated to provide information about the solenoid's state and position.
Redundancy and Reliability:
In critical applications where reliability is paramount, redundancy can be implemented by using multiple solenoids or backup systems to ensure that the desired action occurs even in the event of a solenoid failure.
Testing and Calibration:
Before deploying solenoids in a critical application, conduct testing and calibration to ensure they meet performance and safety requirements. Regular maintenance and testing can also help prevent unexpected failures.
Safety Standards and Compliance:
Ensure that the solenoids you use comply with relevant safety standards and regulations for your industry and application.
Choosing the right solenoid for your application involves considering factors like motion type, force requirements, power consumption, control mechanisms, and environmental conditions. Additionally, regular maintenance and monitoring are essential to ensure continued reliable operation of solenoid-based systems.